What is self-piercing riveting (SPR) and how does it work?
Read on to find out how the SPR process works
How the SPR process works to create a joint
The self-piercing rivet process is a method of joining two or more layers of sheet metal or composite materials with a strong mechanical interlock joint. This process involves using a specialized rivet that cuts through the top layers of material and then flares out into the last layer, forming a permanent and robust connection. It eliminates the need for drilling pilot holes and welding, making it a fast, efficient, and versatile way to assemble various materials while maintaining the integrity of the workpieces. Our self-piercing rivets can securely unite carbon steel, aluminum, copper, and stainless steel sheets with a combined thickness of up to a whopping 0.787" (20mm).
Insert your layers of sheet steel, aluminum or composite into the machine, ensuring the thicker sheet is on the die side for optimal results.
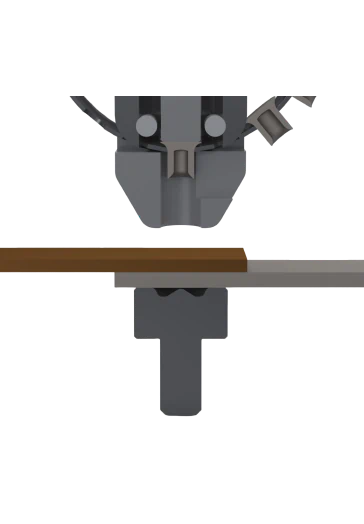
The rivet tooling closes, firmly clamping the workpiece against the rivet die.
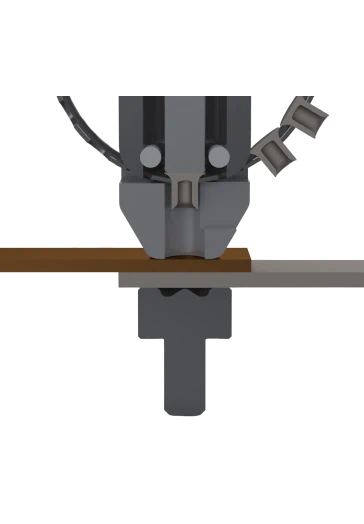
The rivet punch swiftly drives the Self-Piercing Rivet through the layers, cutting through with precision.
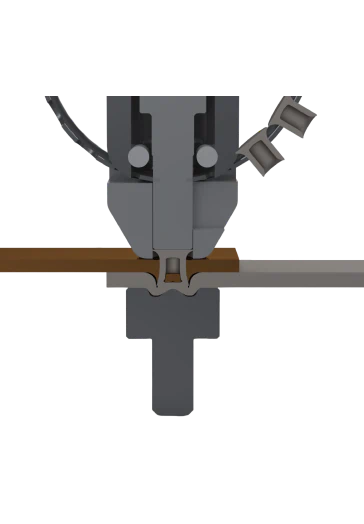
The rivet punch creates a flush finish, and the rivet flares out into the final layer, forming a permanent and sturdy joint.
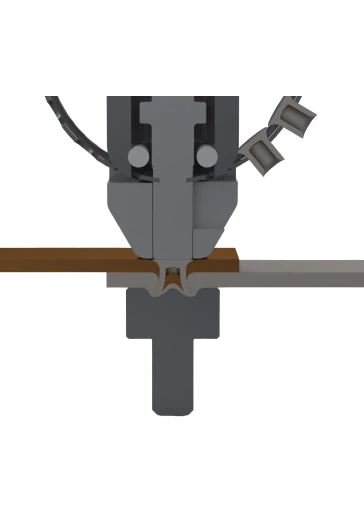
Finally, the rivet punch and holder retract, releasing your perfectly assembled workpiece in a matter of a second (or less).
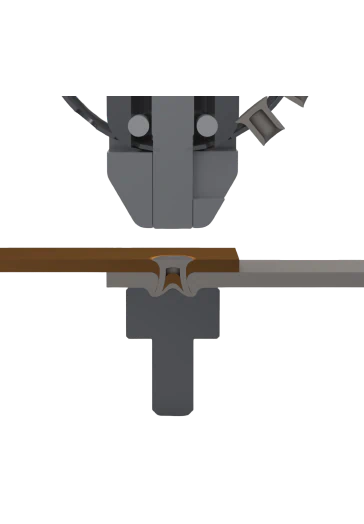
What are the advantages of SPR?
The advantages of SPR:
Low training requirements for operators
Eco-friendly solution, no welding fumes
Strength & versatility
Smooth finish
No pilot hole drilling required
No heat affected zone
Perfect for pre-coated material
Low maintenance
High-speed operation
What kind of tooling is required for self-piercing rivets?
The figure below shows a section of typical SPR tooling. Understanding what each piece of the tooling does will help in troubleshooting and in identifying damaged tooling.
1. Rivet punch: Crafted from durable tool steel, the punch effortlessly drives the rivet through the workpiece, creating a robust joint.
2. Rivet holder: Precisely aligns and holds the rivet in place until it's securely embedded in the workpiece.
3. Workpiece: The layers of sheet steel or composites you wish to join effectively.
4. Self-piercing rivet: Designed to flare out when penetrating the workpiece, forming a robust mechanical joint without the need for a pilot hole.
5. Rivet die: Crafted from tough tool steel, the die clamps the workpiece and facilitates the rivet's flare-out as it enters the material.
6. Rivet feed system (not shown): Our customized rivet feed systems ensure a smooth delivery of self-piercing rivets, tailored to your specific application and budget.
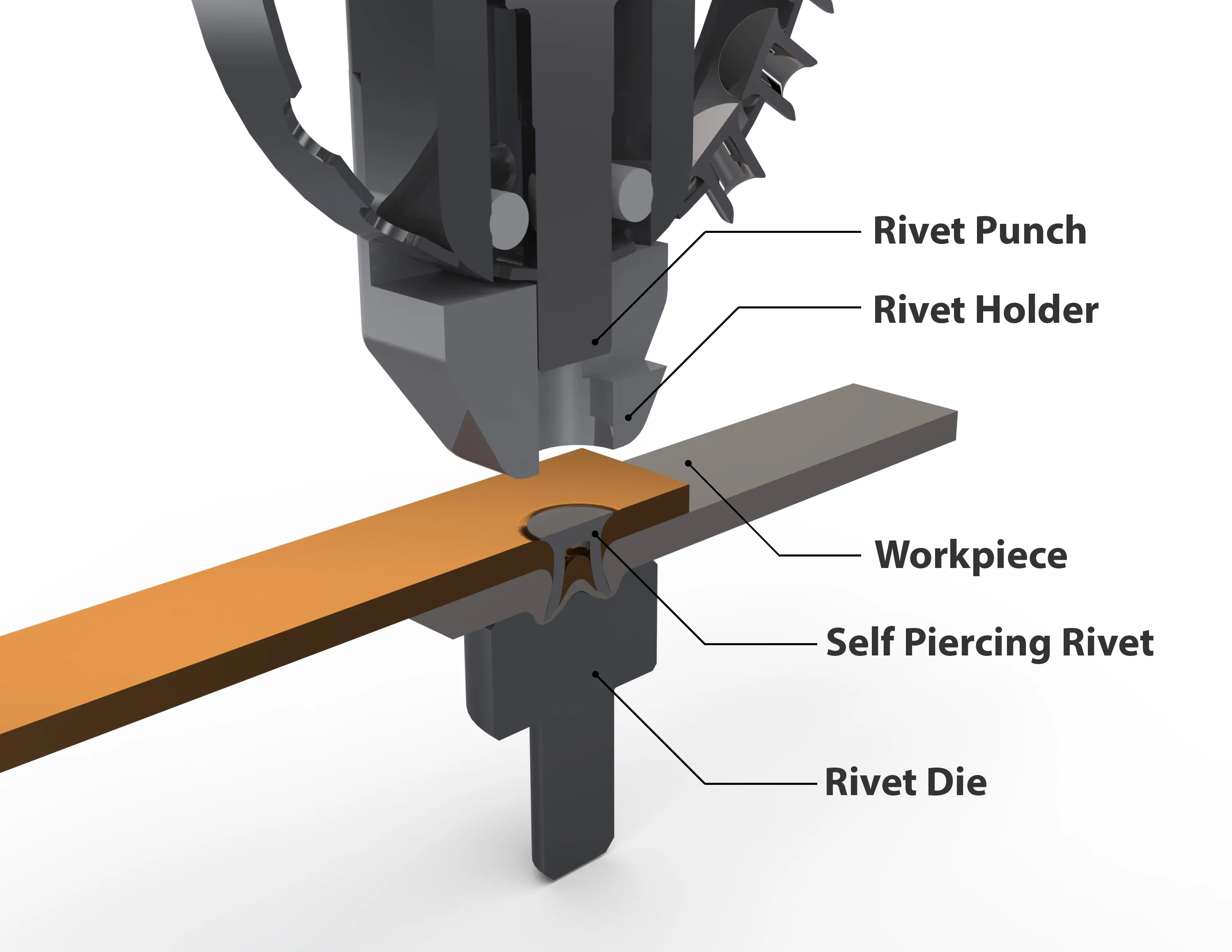
Clinching, welding, or riveting - which is right for your application?
Self-piercing rivets and clinching are non-thermal processes, meaning they do not generate heat during assembly. This eliminates the risk of warping or distortion in materials, making them ideal for joining material that is less than 0.25" (6.3mm) thick or sensitive metals.
Additionally, these methods are faster, requiring significantly less setup time than welding, which can boost production efficiency. Self-piercing rivets and clinching create joints without the need for consumable materials like welding wire or filler metals, resulting in cost savings. They also produce cleaner, more aesthetically pleasing seams, making them ideal for visible or finished surfaces.
It's important to note that welding still has its place in manufacturing. In scenarios where extremely high strength is required, or in applications involving thicker materials, welding may be the superior choice. Moreover, welding offers greater flexibility with a wider range of materials, and it's often the preferred method for critical structural components.
If you're not sure if your part can and should be clinched or riveted, reach out to our team or consider using our sample evaluation process.
Frustrated by inconsistent material joining?
Download your 5 points cheat sheet and troubleshooting guide to improve your results today!